Sport Band, from Early Development to Final Production
| Words by Madeline MyersEarlier today, we launched Glow 2.0, a new and improved version of our best-selling Glow colorway. To celebrate its release, we're taking a closer look at what goes into making the Sport Band you know and love, from early development to producing the bands at our factories.

Early Development
In the early stages of creating Sport Band, our primary focus is ensuring the band fits perfectly on your Apple Watch and on your wrist. Our Product Team uses computer-aided designs, or CAD, to bring the band to life and examine it from every angle, making small adjustments to fine-tune its look and fit.
This iterative process culminates in the creation of prototypes, or early models, of the band. We test the prototypes on wrist-shaped blocks of plastic, striving for that sweet spot between universal usability and individual comfort.
What's It Made Of?
When it came to selecting the material for Sport Band, we knew we wanted something comfortable and durable. Fluoroelastomer rubber, or FKM, is costly and can be quite challenging to work with but it quickly emerged as a winner. Unlike the more commonly used silicone, FKM offers superior strength, durability, and a silky, cloud-like feel. It easily contours around your wrist and it resists oils, making it an ideal choice for active applications (running, biking, surfing, you name it).
Sport Band features an aluminum pin and tuck closing mechanism that is both slim and secure. The aluminum pin latches through the band while the tail end tucks neatly against your wrist.
Everything about this band is intended to be light, minimal, and simple, and we worked through a ton of concepts to keep that ethos alive. We wanted to separate Sport Band from the earlier and slightly bulkier Rugged Band.
Why Sport Band?
We asked two of our Product Managers: “Why pick Sport Band over any other band on the market?” They walked us through several key features of the band, and highlighted how each resolves potential pain points for customers.
- Premium Material: Molded from compression-molded FKM, Sport Band offers unparalleled durability without compromising comfort. It’s soft and silky, and contours around your wrist.
- Secure Fit: Sport Band securely locks into all series of Apple Watch, making it ideal for strenuous outdoor activities.
- Longevity: Unlike coated alternatives, Sport Band is made of a solid piece of FKM to ensure color retention and resistance to wear over time.
- Ease of Use: The pin and tuck mechanism strikes the perfect balance between convenience and security.
- Comfort: Ventilation channels stretch across the width of the band and minimize moisture buildup, while the texture offers a soft, luxurious feel.
Every component of the band, from its metal lug latches to its innovative closing mechanism, was custom designed by our Product Team. We wanted to design a band that we’d feel confident adventuring with. From surfing Rincon to mountain biking in the Santa Ynez range, you’ll find our team members out and about with Sport Band every weekend.
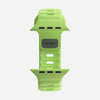
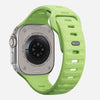
To the Factory
Once development is finished, we send Sport Band off to the factory for production. Here’s what it looks like in a few steps.
- The raw FKM is procured from the supply chain and arrives at our factory already dyed to our chosen color.
- Our factory cuts the FKM into pieces of a specific weight which are then placed into a mold.
- The FKM is compressed under very high pressure and temperature for several minutes, transforming it from shapeless rubber into a hard and strong material that holds its form.
- The bands are removed from the mold and trimmed down one by one.
- They are then flash frozen and trimmed again for high precision.
- The metal and lug components are then assembled and the bands move through a series of quality control checks (see below).
- The Sport Bands are packaged by hand, then sent off to our fulfillment centers for shipping!
At Nomad, quality control is a top priority throughout our production process. Our rigorous standards begin with inspections at the factory, followed by thorough evaluation by our team at our Santa Barbara headquarters. We meticulously ensure that each band meets our quality standards. Any bands that fall short of these standards are reworked by the factory to ensure they pass through a second round of inspection.

It's Not Without Challenges
The FKM rubber we use for Sport Band presents difficulties in manufacturing – it’s much harder to work with and it’s much more expensive than silicone. Despite these challenges, our decision to use FKM stems from its inherent qualities that contribute to elevating the overall quality of the product. In short, it isn’t the easiest to work with, but it’s the best material on the market.
Colorway Creation & Glow 2.0
Our colorways are largely determined by our Design Team. They build out a vision of the product lineup and then the Product Managers refine what the exact colors end up being through moodboarding and sampling. It’s a collaborative process that relies on the expertise of multiple teams.
The transition from Glow 1.0 to Glow 2.0 marked a significant shift in our approach to luminous materials. While the development of Glow 1.0 was relatively quick, Glow 2.0 required more extensive effort and exploration. We conducted thorough sample testing, reviewing over 20 iterations to refine various aspects such as base and glow colors, FKM pigment density, and luminosity strength. We drew inspiration from nostalgic glow-in-the-dark products from the 1990s and early 2000s (think glow-in-the-dark ceiling stars).

Glow 2.0 is now available for 40mm/41mm and 45mm/49mm Sport Band and iPhone 15 Pro and iPhone 15 Pro Max Sport Case. It’s one of our Limited Edition colorways, so it won’t be around for long (our first Glow colorway sold out in less than 12 hours!).
Full Steam Ahead
We’re not stopping here. Our Product Team plans to build out entirely new waterproof FKM, and experiment with other materials colorways as well. We love hearing from you! Get in touch with us at support@nomadgoods.com.